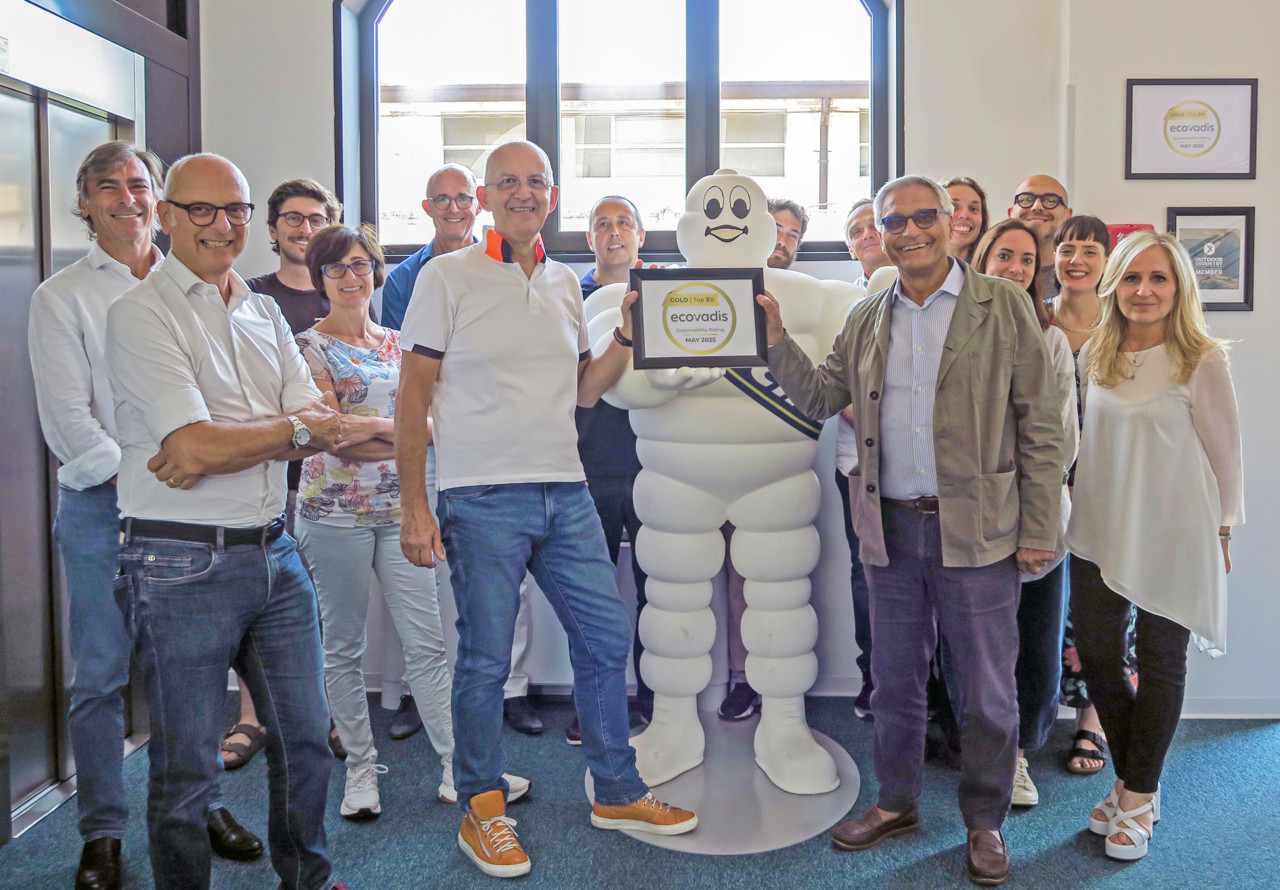
JV International wins EcoVadis Gold Medal
JV International stands out in the Italian industrial landscape, joining the elite 5% of over 130,000 companies assessed globally over the last 12 months.
Keep reading...The Vigevano-based company has been a leader since 1952 in the production of natural para rubber for footwear, using a special technologically innovative process that guarantees high quality and respect for the environment.
February 2024
The story of GEA GOMMA SRL is a family history, but also a story of commitment to the pursuit of quality by drawing on the natural heritage. In fact, the company was founded in Vigevano in 1952 on the intuition of Giuseppe Bonomi, who realised the potential of natural rubber for footwear production. This is how GEA GOMMA soon became a European leader in the production of natural rubber for footwear, an activity that is carried on today with commitment and success by the founder’s children: Daniela Bonomi, flanked by her three sons, William, Paola and Stefano Grivel.
The production complex we see today is the result of the expansion that took place in 1969, with the transfer of the business to Castello d’Agogna. In the industrial warehouses, which occupy an area of about 14,000 square metres, the entire process of manufacturing natural rubber, known internationally as ‘sole crepe’, takes place. The manufacturing process of the rubber soling sheets follows a strict and precise specification, which aims to guarantee the highest product quality and total respect for the environment.
The special processing to which natural rubber for footwear is subjected is technologically innovative, making GEA GOMMA one of the leading brands in the footwear accessories sector.
The manufacturing process of natural para rubber is environmentally friendly and non-polluting, consisting of the processing of natural raw rubber obtained from the latex of the Hevea Brasiliensis plant. The latex is purchased from plantations in South-East Asia, which produce the best quality rubber, and by means of mills, mixers and calenders, the raw rubber is processed into sheets of different thicknesses and colours. This process not only produces shoe soles of the highest quality, but also a rubber that is not chemically treated and retains its characteristics. This process, moreover, has the added value of not producing fumes, vapours, dust, and environmentally polluting waste. Moreover, any processing residue can be reused in the production cycle.
JV International stands out in the Italian industrial landscape, joining the elite 5% of over 130,000 companies assessed globally over the last 12 months.
Keep reading...The Italian company, a benchmark for the production and marketing of high-tech adhesives and fabrics, also stands out for its high level of management.
Keep reading...Four decades of collaboration between DESMA and ABB have transformed automation in the footwear industry. From the first robots adopted in the 1980s to today's solutions, the synergy focuses on efficiency, precision and sustainability for shoe manufacturers around the world.
Keep reading...You must login to read this free content
This content requires a subscription to view. Are you already a subscriber? Sign in