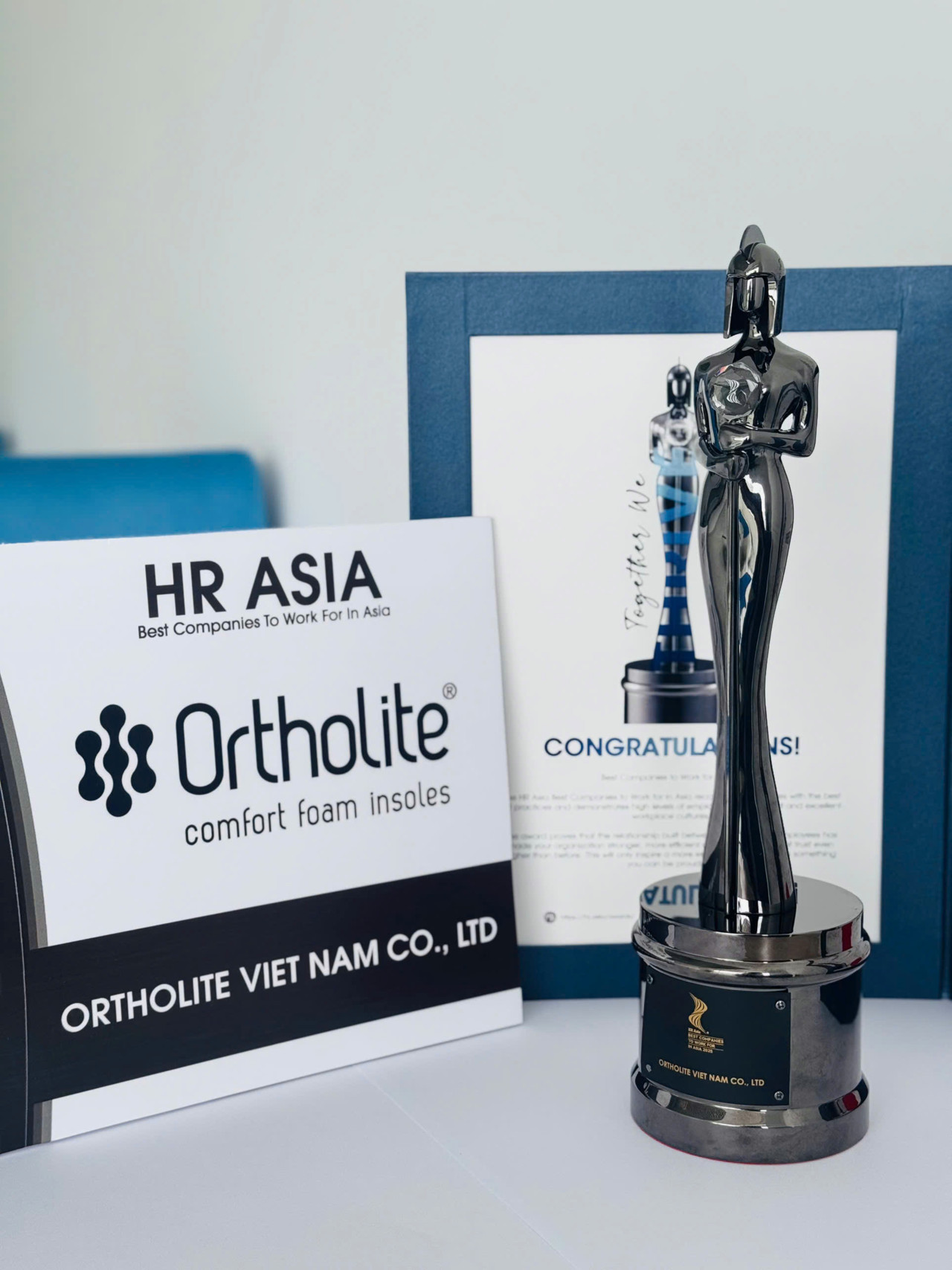
OrthoLite Vietnam: among Best Places to Work in Asia
During a ceremony in Ho Chi Minh City on August 14, OrthoLite Vietnam has been recognized, for the second year in a row, among the best companies to work for in Asia by HR Asia .
Keep reading...INNOVERA™ is made using plant proteins, biopolymers and recycled rubber, for a renewable carbon content of over 80 per cent, and is 25 per cent lighter and twice as strong.
April 2025
Modern Meadow, a leader in sustainable materials, announced that designer Karmuel Young used the company’s biomaterial in his nomination for the Sustasia Fashion Prize. Young, who lives in Hong Kong, chose to use Modern Meadow’s INNOVERA™, formerly known as BIO-VERA®, in his four-in-one suit, which can transform from a jumpsuit to a long coat, short jacket and trousers.
Organised by the Shanghai Fashion Designers Association and yehyehyeh, the Sustasia Fashion Prize 2025 aims to accelerate sustainable practices and innovation in the fashion industry in Asia.
“We are honoured that Karmuel Young chose to use our INNOVERA™ biomaterial in his design for the Sustasia Fashion Prize, so as to showcase the beauty and versatility of innovative and sustainable materials in clothing,” said David Williamson, PhD, CEO of Modern Meadow.
But let’s start with the basics. Let’s ask what the novelty proposed by Modern Meadow presented at the February 2025 edition of Lineapelle consists of. Pierluigi Berardi – VP, Head of Sales & Marketing at Modern Meadow tells us about it.
Introducing Modern Meadow, which took part in Lineapelle for the first time in February 2025.
“Founded in 2011 and based in Nutley, New Jersey (USA), Modern Meadow designs innovative biomaterials inspired by nature. Its products, made using a new hybrid material composed of plant proteins and bio-based polymers, are sustainable, stronger and lighter than traditional materials. Modern Meadow aims to reduce dependence on animal and petroleum-based products without sacrificing quality. The materials integrate seamlessly into existing production processes of the footwear, accessories and fashion, automotive and furniture industries. By collaborating with prestigious brands such as Tory Burch and industry leaders such as BASF, Bader and ISA TanTec, Modern Meadow guarantees high quality and fully traceable products.”
What is INNOVERA™?
“INNOVERA™ is designed to mimic the effect of collagen in the skin. It is made using plant proteins, biopolymers and recycled rubber, for a renewable carbon content of over 80%, and is 25% lighter and twice as strong as leather. It can be customised in colour, feel and pile, depending on the designer’s preferred use.”
This performance I guess comes from the way the product is constructed….
“The product is made of a Nylon 6 nonwoven substrate obtained from recycled tyres, thanks to a collaboration with BASF.
We obtained the polymer from them, which was spun and transformed into fibres to then make up the nonwoven fabric. This was engineered in such a way that it could be impregnated with the plant- and bio-based polymers (soy protein and polyurethane, respectively) and not have any empty space (hence the high strength of the material). If you cut the finished material, in fact, it is virtually impossible to detect the nonwoven fibres.”
What was your goal in making INNOVERA™?
“Our aim was to provide the tanning world with a neutral canvas, with impeccable performance, capable of expanding the product offering, without having to invest in any new technology, but by using the resources and knowledge already in the tanneries’ toolbox.”
Shall we explain its qualities in more detail?
“The material can be categorised as ‘next-gen material’. Materials capable of associating the concept of sustainability with that of performance. Materials, therefore, not only suitable for capsule collections, but also perfect for mainstream use.
It is a winner to be able to combine the precision and performance of an artificial material while maintaining the creative characteristics of traditional finishing processes.
The main benefits it provides are: total freedom in design with less waste; a traceable supply chain; high performance; recycling and sustainability.
To these are added many other benefits. Its processing eliminates resource-intensive tannery processes. In fact, shaving, desalting, tanning and retanning are eliminated, starting with the finishing stages. The panels are absolutely uniform in colour rendering. Any colour can be obtained and any finish applied, resulting in a wide variety of coats and tactile sensations. At the fair we also brought examples of embossing or perforation. Even the smell is close to that of a natural product, as soya proteins react to tanning in a similar way to animal proteins. The panels are perfectly squared and have no areas to discard; therefore, the highest possible yield is produced. Time is saved by eliminating the steps of initial selection and final inspection of the material, as well as the evaluation of defects in preparation for cutting.”
Can you support the demands of the market?
“Modern Meadow is able to commercially produce more than 500,000 square metres per year, making it readily available to customers and simplifying supply chain issues. This is also because INNOVERA™ requires no special preservation or storage conditions, reducing complexity and costs, and has scalable adoption. It can easily complement and shorten existing production processes and allows designers and leather experts to produce customised materials.”
When it comes to sustainability, today we talk in particular about circularity as well as the use of recycled materials. What does the end-of-life of INNOVERA™ look like?
“The first tests we have conducted, which are not yet conclusive, indicate that a little over 50% of INNOVERA™ can be recovered at the end of its life.”
What set of certifications accompanies INNOVERA™?
“The product supplied by BASF is ISCC certified, while for the finished material we are working to achieve Cradle-to-Cradle (C2C) certification and to produce an LCA study.”
Costs?
“We position ourselves on a par with a mid- to high-end leather, but without the waste that has to be considered in the case of a leather.”
What future developments can we expect?
“We are testing the product, with excellent results, in relation to the world of safety footwear. Later on, we will also propose other thicknesses – in addition to the current 1.1-1.3 – which will allow us to adopt them also for linings or reinforcements.”
During a ceremony in Ho Chi Minh City on August 14, OrthoLite Vietnam has been recognized, for the second year in a row, among the best companies to work for in Asia by HR Asia .
Keep reading...JV International stands out in the Italian industrial landscape, joining the elite 5% of over 130,000 companies assessed globally over the last 12 months.
Keep reading...The Italian company, a benchmark for the production and marketing of high-tech adhesives and fabrics, also stands out for its high level of management.
Keep reading...You must login to read this free content
This content requires a subscription to view. Are you already a subscriber? Sign in