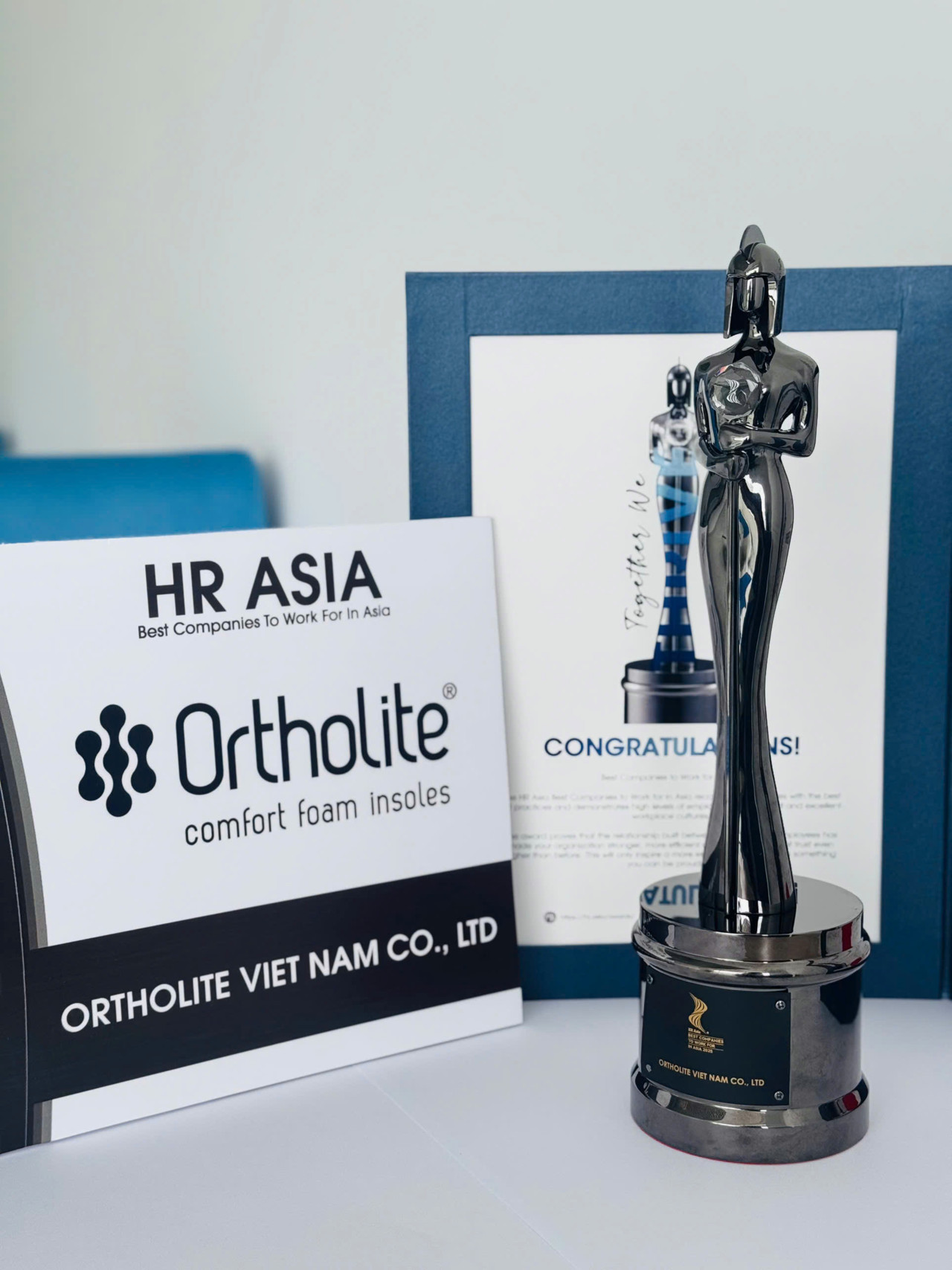
OrthoLite Vietnam: among Best Places to Work in Asia
During a ceremony in Ho Chi Minh City on August 14, OrthoLite Vietnam has been recognized, for the second year in a row, among the best companies to work for in Asia by HR Asia .
Keep reading...A shining example of how collaboration and innovation can truly shape the future of sustainable footwear. Discover the project by Balena, framas and Moon Rabbit Adaptive Lab.
May 2025
Technology, sustainability and design met at Milan Design Week 2025 during the ‘Walk Wise’ talk, moderated by Matteo Pasca, director of Arsutoria Studio and Arsutoria School. The panel, held at Isola Basic Village, explored how the footwear industry is rethinking materials, processes and shoe construction to reduce its environmental impact, particularly when it comes to end-of-life shoe solutions.
Pasca opened his talk by highlighting the main trends in the global footwear market and the complexity of designing models with circularity in mind, especially considering the multi-material nature of most shoes. Presenting the FootLoop project – single-material shoes, alternative constructions and biodegradable materials – were three speakers. Each representing one of the 3 leading companies in the sector that initiated the research and development of the project.
René Medel – Senior Digital Creation Engineer at framas Group, a leading manufacturer of high-performance plastic components for the sports footwear industry. Jesus Marini Parissi – Founder of Moon Rabbit Adaptive Lab, which fuses computational design, advanced engineering and systems optimisation. Yael Joyce Vantu – Chief Product Officer of Balena, a pioneer in the development of circular materials and biodegradable solutions for fashion and footwear.
WHAT IS FOOTLOOP?
Footloop is a fully modular, mono-material shoe system, built using Balena’s compostable BioCir® material and designed to perform through both 3D printing and injection molding. The concept was guided by three core principles:
Modularity: components can be replaced, repaired, or disassembled without adhesives.
Materiality: a single circular material is used throughout.
Movement: the shoe is engineered for comfort, flexibility, and real-world performance.
The result is a shoe that redefines how we make, use, and unmake footwear, pushing the boundaries of both design and sustainability.
DESIGNING WITH SYSTEMS IN MIND: MOON RABBIT LAB’S APPROACH
As experts in computational design and digital fabrication, Moon Rabbit Lab approached Footloop not as a finished product, but as a living system, one that could adapt, move, and return to nature without leaving waste behind.
“We saw Footloop as an opportunity to redesign footwear from the inside out,” Jesus Marini Parissi shared. “Rather than layering materials or bonding incompatible parts, we focused on using a single compostable polymer, Balena’s BioCir®, to create a fully modular, multi-component shoe.”
Moon Rabbit’s design process was rooted in biomimicry and systems thinking. Drawing inspiration from natural structures, leaves, shells, and branches, they used computational tools to create geometries that were lightweight, flexible, and strong.
Each part was optimized for performance through virtual simulations before being physically prototyped. “We built digital twins for every component,” he explained. “That allowed us to run simulations, tweak performance variables, and test tolerances long before printing a single part. The material wasn’t just a passive input; it actively influenced the form.”
MANUFACTURING INNOVATION WITH FRAMAS
Known for their leadership in footwear tooling and component manufacturing, framas played a crucial role in translating design ambition into physical function. Their core challenge was to integrate a 3D-printed upper and sole both produced with Balena’s BioCir® with an injection-molded outsole, all without adhesives or chemical bonding.
“We had to fundamentally rethink how a shoe is constructed,” René Medel said. “Instead of gluing or fusing components, we designed them to lock together mechanically. This required going back to traditional shoemaking methods pre-industrial construction techniques where craftsmanship drove function.”
This mechanical interlocking system not only supports disassembly and repair but also enhances circularity by eliminating composite waste. Every connection is intentional and reversible. From a manufacturing standpoint, framas also validated BioCir® across two major platforms:
In injection molding, the material is handled similarly to thermoplastic polyurethane (TPU), making it easy to integrate into existing production lines.
In FDM 3D printing, however, success depended on detailed parameter calibration,highlighting both the challenges and the opportunities of working with innovative circular materials.
BALENA’S MATERIAL AT THE CORE
At the heart of Footloop is Balena’s BioCir®, a flexible, compostable, and bio-based material designed for circularity without compromising performance. Unlike traditional polymers, BioCir® is engineered to meet the demands of industrial manufacturing while enabling multiple end-of-life pathways from recycling to composting.
What set this project apart was the ability to apply the same material across both additive and conventional production processes. Whether in filament or pellet form, BioCir® offered the durability, elasticity, and processability required to prototype, refine, and ultimately manufacture a fully modular shoe.
A NEW LOOP FOR FOOTWEAR
Footloop is more than a shoe, it’s a statement. It challenges the footwear industry to think beyond products and toward systems. From computational modelling and modular design to bio-based materials and regenerative end-of-life strategies, it shows what’s possible when collaboration replaces compromise.
Balena, framas and Moon Rabbit Adaptive Lab didn’t just create a shoe. They created a new way forward.
During a ceremony in Ho Chi Minh City on August 14, OrthoLite Vietnam has been recognized, for the second year in a row, among the best companies to work for in Asia by HR Asia .
Keep reading...JV International stands out in the Italian industrial landscape, joining the elite 5% of over 130,000 companies assessed globally over the last 12 months.
Keep reading...The Italian company, a benchmark for the production and marketing of high-tech adhesives and fabrics, also stands out for its high level of management.
Keep reading...You must login to read this free content
This content requires a subscription to view. Are you already a subscriber? Sign in