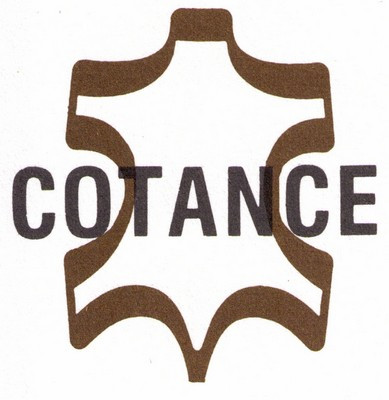
Germany: “apple leather” label banned
German tanning association (VDL) wins major victory in court
Keep reading...May 2025
Recycling is at the heart of the Bioshoes4all project, ‘Innovation and empowerment of the footwear sector for a sustainable bio-economy’, because the use of recycled materials is one of the strategies with the greatest impact on reducing the environmental footprint of products.
Coordinated by APICCAPS and the Footwear Technology Centre of Portugal and supported by the PRR (Recovery and Resilience Plan), Bioshoes4all’s project ‘Innovation and empowerment of the footwear sector for a sustainable bio-economy’ places recycling as one of the main priorities in order to develop a sustainable economy for the footwear sector and reduce the environmental footprint.
While global plastics production has increased significantly in recent years, reaching around 430 million tonnes in 2024, only 9% of this production is recycled.
The consumption and production of plastics requires the use of large amounts of fossil fuels, which has a negative effect on the environment. To make matters worse, the decline in economic activity has led to a sharp fall in the global price of oil, making the production of plastics from virgin fossil materials significantly cheaper than the use of recycled plastics. According to the European Environment Agency, if the production and use of plastics continues to grow as predicted, the plastics industry will be responsible for consuming 20% of the world’s oil by 2050, a significant increase from the current 7%.
The ever-increasing amount of plastic, its impact on biodiversity and its contribution to climate change, as well as its integration into a circular economy, are all issues on the footwear and leather industry’s agenda.
RECYCLING FOR 100% CIRCULARITY
Recyclable material is a material that is collected, reprocessed and used in the production of recycled materials. Plastic materials can be recycled several times through extrusion (reprocessing process) and injection (mechanixal forming), metal materials can be melted down and reprocessed to produce new materials, and fibres can be extruded to produce new yarns.
In the footwear cluster, for example, waste from the production of thermoplastic polyurethane (TPU) and thermoplastic rubber (TR) soles can be collected, crushed and reformulated (adding additives if necessary to ensure the properties required for function) for injection into new footwear components. These materials can be recycled several times while maintaining their functional properties.
Post-consumer waste, materials or products discarded by consumers at their end-of-life, can be collected, sorted, and reprocessed to create new recycled materials for product manufacturing. Multiple methodologies are available for the recycling of these materials, such as the development of dedicated recycling processes for individual material types, the production of composite materials, or the recycling of thermoplastic materials, among others. Another, still in its infancy but with potential, is the recycling of post-consumer footwear which, after collection, sorting and separation of materials, can be ground, and the resulting material is used to develop new materials/components for footwear or other applications such as flooring or construction. The recycling process is facilitated in products with less material diversity and by using materials of the same type and similar composition.
The use of recycled materials in the production of footwear is one of the strategies with the greatest impact on reducing the environmental footprint of products, both by reducing the extraction and consumption of raw materials and by reducing the amount of waste sent to landfills or incineration.
Bioshoes4All is researching and developing various approaches for the recycling and valorization of footwear waste (post-production and post-consumer). These include, among others, the recycling of thermoplastic and thermoset materials for shoe soles; the production of textile-based composite materials for footwear and leather goods; the development of composites for insoles and soles; and the development of non-woven materials and construction materials, incorporating footwear waste. The project is also studying the implementation of a collection model for post-consumer injected footwear, with a view to its reprocessing and production of new footwear products.
By the end of the year, a new generation of products will be completed.
German tanning association (VDL) wins major victory in court
Keep reading...Il primo trimestre 2025 si apre in salita per la pelletteria italiana: export giù dell’8,5%, produzione in calo a doppia cifra e domanda interna ancora stagnante. Il comparto, nonostante un saldo commerciale positivo, fatica a ritrovare lo slancio. A pesare sono i conflitti internazionali, l’incertezza economica e i dazi USA.
Keep reading...From July 2025, Federica Bevilacqua will take on the role of general manager of both Assopellettieri and Aimpes Servizi.
Keep reading...You must login to read this free content
This content requires a subscription to view. Are you already a subscriber? Sign in